2019年07月30日
【Bianchi】ベルガモ郊外のビアンキ本社を訪問。クオリティコントロールへのこだわりを知る
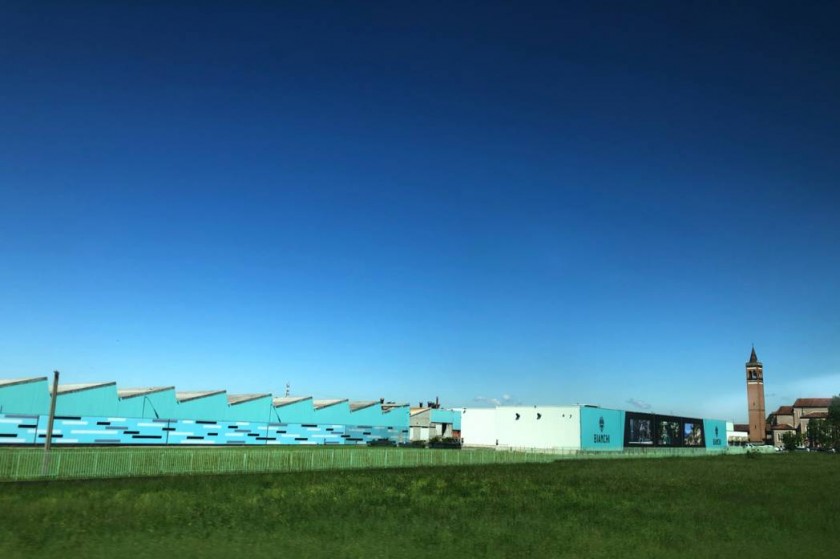
先日行われたGranfondo Felice Gimondi Bianchiの翌日に、ベルガモの郊外にあるビアンキ本社を訪問した。
澄み切った青空にチェレステカラーの社屋が映える。なるほど、ビアンキのコーポレートカラーの生まれた由来がこの青空と言われれば納得。ビアンキの長い歴史を感じさせるモダンな建造物だ。
創業時、ミラノのヴィア ニローネ7(via nirone 7)にあったオフィスの現在はアパートメントとなりその面影はないが、ここにはビアンキの総本山たるべく威風堂々とした社屋が立つ。お世辞にも最新の建造物とはいえないが、幾多の困難にも立ち向かい乗り越えたからこそ現在もなお、その姿を拝することができる。この創業140年という歴史はダテではないのだ。
正面にはそのプランドを表すかのような大きなビアンキの看板を掲げている。エントランスは改修したばかりといい、モダンさを生かしたデザイン。
3台のバイクが来訪者を出迎えるようなスタイルだ。
まず先に通されたのは、2020年モデルが展示されているホールだ。ここは写真撮影は禁止。なるほど来季のトレンドはこうなってなるのか…..。ユーザーの皆さんはもうしばらくお待ちを。
こちらはファクトリーアウトレットコーナー。ショップのようなしっかりとしたディスプレイ。
そしてファクトリーへ。
現在ビアンキの製造工場は世界で10箇所あるという。ここはまさにビアンキの製造拠点だ。
うずたかく積まれている完成車箱。出荷を待つハイエンドモデルたちだ
ファクトリーの仕組みについて、説明をうけている一行。
現在の工房では、ロードバイク、マウンテンバイク、そしてeBikeなどのハイエンドモデルのみパーツアッセンブルを行なっている。年間およそ2万台のバイクがここで組み付けられている! 過去には最大で40万台のバイクがここから出荷されていたという。
現在27人の職員がバイクの製造を行なっており、その作業にはこだわりがあるという。それは分業(流れ作業)ではなく1人が1台のアッセンブリーをすべて責任をもって行うということ。バーコードで担当者や、製造ナンバーを記録しており、製品の管理が行き届いている印象だ。
また、時代の変化とともに新しいシェアも増えおり、本社での製造を増やす計画もあるという。eBikeが好調で、e-マウンテンバイクに関心をもっているようだ。
電動アシスト装置を付加したスポーツバイクがイタリアを含めたヨーロッパでは人気を集めているという背景がある。
ビアンキもeBikeの開発には積極的だ。見かけはロードバイクと大きく変わらないが、モーターアシストユニットを搭載したロードバイクのアリアはまさに、市場のニーズに応えるためのバイクといえる。現段階においてEU圏でしか使うことができないモーターアシストユニットを用いているので、日本では乗ることができない。
カーボンフレームを製造する際には金型が必要だが、金型自体を製作するコストもかかる。そのため3Dプリンターで出力し、実験し最終的なフレームデザインが決まった段階で金型を製作する。新製品を生み出すためには膨大なコストがかかるので簡単にはいかないそうだ。反面、一台一台じっくりと作り上げているという印象もうける。
こちらは3Dプリンターを用いてレジンで出力したモックアップ。手前のオルトレXR4は綺麗に塗装されているので、一見製品と思ってしまうが、レジンでできた100%サンプルだ。製品として流通させても良いレベルになるまで、このような作業を繰り返しおこなっている。
撮影禁止のラボでは….
研究施設、すなわちラボは撮影禁止。どのような空間であるかテキストでお伝えしよう。
施設内に設けられたブースに仕切られた空間で、外部とは遮断されており入室は制限されている。ブース内はおよそ20平米といったところか。ドアを開けると、すぐに目に飛び込むのは複数の試験機だ。各試験機にはフレームがセットされ、振動が加えられているのがわかる。内部は整然としているが、テストを受けた、あるいは受けるのを待っているであろう製品が並び、自転車機材好きであれば興味を惹くもので溢れた空間だ。全般的にいえるが問題が生じリコール・商品回収というニュースが日常生活の中でも流れてくる。ビアンキは製品を出す以上は、製品のテストを休むことなく連日に渡り実施する。そこで何か問題が生じればいち早くカスタマーへ伝え対策を講じる。
多くのメーカーは生産工場で耐久テストを行なっているが、ビアンキは生産工場と本社でもテストを行うダブルチェックというスタイルがポリシーだ。テスト基準はISO基準に則った方法がベーシックだが、本社ではISO基準を越えた基準を設けたテストも行なっているという。厳しい自社基準をクリアした製品だけが世の道路を走ることができるのだ。こと安全性にかんしてはもっとも時間と費用をかけているのだという。
高い製品基準だけではなく、3つの大切なことがあるという。
実にイタリアンメーカーらしいが、恰好よくないといけない。
そして重さ。最近ではディスクブレーキによって重量増の傾向もあるので軽くしていきたい。
最後はスフィテフネス。必要な強度があるかどうか。スプリントをしたときにしっかりと力が加わるか。しかしあまり固すぎても乗りづらくなってしまう。最適な強度のバランスを重要視しているのだという。
チームを持つ重要性©︎サイクルヨーロッパジャパン
先日行われたジロ・デ・イタリアでは総合3位となったプロモシュ・ログリッチ
現在、ビアンキを供給しているチーム・ユンボヴィズマは非常に好調で、前半シーズンであるにも関わらず昨年を上回る勝利数を挙げている(2019年7月現在)。このチームを持つメリットとしては選手から様々な意見が寄せられるが、トップレベルの環境から寄せられた最新の意見を製品開発に取り入れられるというのは、まさに強みといえる。
ビアンキのカラーオーダーシステム”ビアンキ タボロッツァ”はここで創られる
上位機種“レパルトコルサ”だけに施すことができるカラーオーダーシステム“タボロッツァ”は、まさにこのペイントブースで行われているという。訪問当日は作業を見ることはできなかったが、ブース内部を見学できることに。ブース内部には一部にマスキングシートが残っており、淡くチェレステの塗料で染まっているのが確認できる。ついさっきまでペイントをしていたのではないか、という臨場感がある。クリーンさを保つ必要がある場所なので、撮影をさせていただき早々に退散。
ビアンキ ミュージアム併設を見学
歴史的な展示品を間近で見られるミュージアム。時系列で並べられておりビアンキの歴史を順を追ってたどることができる。エントランスには創設者エドアルド・ビアンキの銅像、さらにはオブジェが出迎えてくれる。
左は1899年グランプリ・ド・パリで優勝した、ジョヴァンニ・トマッセッリのバイク。右のこちらはあのファウスト・コッピのバイク。1953年の世界選手権を制したバイク。
左のバイクは1973年の世界選手権で優勝したフェリーチェ・ジモンディのバイク。右のマウンテンバイクは、ジュリアン・アプサロンが2004年アテネオリンピックで金を獲ったときのもの。
ミュージアムの案内をしてくれたのはクラウディオさん。日本のスタッフとも気のおけない仲だ。
雑誌などで目に焼き付けたモノトーンだった記憶が原色で蘇る。まさにノスタルジー。ファウスト・コッピ、フェニーチェ・ジモンディ…..教科書の中の偉人が駆ったバイクが目の前にある。
ビアンキコレクター垂涎のキャラクターグッズや、アメニティはファンならずとも欲しくなってしまいそう。要望がよせられたら復刻しませんか??
取材協力:サイクルヨーロッパジャパン
関連URL:http://www.japan.bianchi.com/
著者プロフィール
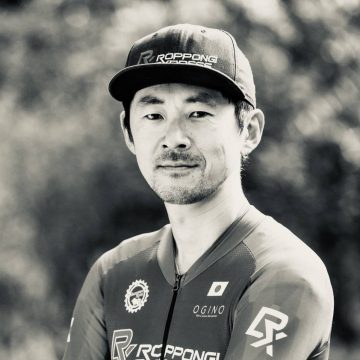
山本 健一やまもと けんいち
FUNRiDEスタッフ兼サイクルジャーナリスト。学生時代から自転車にどっぷりとハマり、2016年まで実業団のトップカテゴリーで走った。自身の経験に裏付けされたインプレッション系記事を得意とする。日本体育協会公認自転車競技コーチ資格保有。2022年 全日本マスターズ自転車競技選手権トラック 個人追い抜き 全日本タイトル獲得